Understanding the inner workings of an engine can feel complex, but when it comes to boosting efficiency and performance, few components play as vital a role as rail injectors. Whether you’re curious about how modern engines achieve such impressive fuel efficiency or you’re working directly with diesel engines, rail injectors are key players in the process.
What Are Rail Injectors?
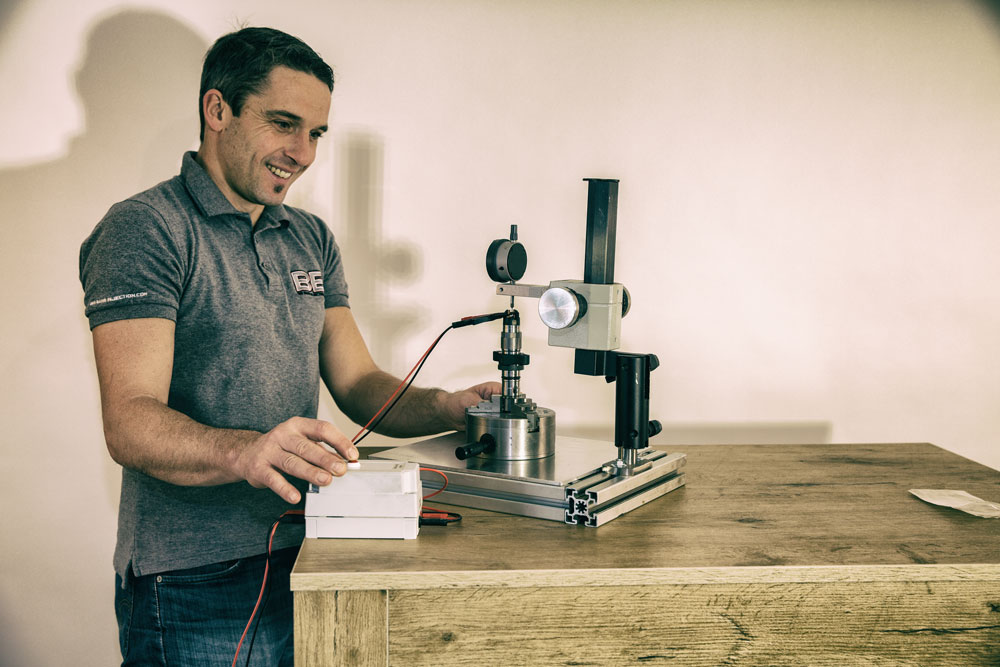
Rail injectors, often part of a common rail fuel injection system, are precision-engineered devices responsible for delivering fuel into an engine’s combustion chamber. Unlike older fuel injection systems, which relied on mechanical timing and limited control, rail injectors from the likes of Austrian company Big Bang Injection work in tandem with an electronically controlled common rail. This common rail is a pressurized fuel reservoir that supplies the injectors with a consistent, high-pressure fuel source.
The rail injectors themselves are designed to inject the right amount of fuel at precisely the right moment, down to milliseconds. This precision ensures optimal combustion, leading to better performance, fuel economy, and reduced emissions. Rail injectors are commonly found in diesel engines but have also made their way into some high-performance petrol engines.
Key Features of Rail Injectors
- High-pressure delivery – Rail injectors operate at extremely high pressures, often exceeding 2,000 bar. This ensures the fuel is atomized into a fine mist for even and efficient combustion.
- Electronic control – Modern rail injectors are electronically controlled, allowing precise adjustments to fuel timing and volume based on engine conditions.
- Multiple injection events – Rail injectors can deliver multiple pulses of fuel during a single combustion cycle, helping to improve performance and reduce noise.
- Durability – Built to withstand high pressures and intense heat, rail injectors are made from durable materials like hardened steel or advanced alloys.
- Compatibility with emissions systems – Rail injectors are crucial for meeting modern emissions standards, as they enable the precise fuel-air mixture needed to minimize pollutants.
How Do Rail Injectors Work?
The operation of rail injectors revolves around precision and efficiency. Here’s how the process unfolds:
- Fuel pressurization: The fuel is pressurized within the common rail, which is powered by a high-pressure fuel pump. This ensures a steady supply of fuel at the correct pressure.
- Electronic signals: Sensors monitor various engine parameters like speed, load, and temperature. This data is sent to the engine control unit (ECU), which calculates the ideal timing and amount of fuel to inject.
- Injection process: The ECU sends a signal to the injector, which opens a valve to spray the pressurized fuel into the combustion chamber. The fuel is atomized into a mist to ensure complete combustion.
- Multiple injections: Depending on the engine’s requirements, the injector may perform several injections during a single cycle. For example, a pre-injection event might occur to smooth out combustion, followed by the main injection and sometimes even a post-injection to reduce emissions.
This level of control not only improves efficiency but also enhances engine responsiveness and reduces unwanted noises like knocking.
How Rail Injectors Improve Engine Performance
Here’s how:
- Optimized combustion: By delivering the right amount of fuel at the perfect time, rail injectors ensure that combustion is as efficient as possible. This leads to more power from the same amount of fuel.
- Improved fuel economy: Precise injection reduces fuel wastage, allowing engines to run more economically.
- Reduced emissions: Combustion efficiency directly impacts emissions. Rail injectors allow for cleaner burning, helping engines meet stringent environmental standards.
- Better responsiveness: The ability to adjust fuel delivery in real-time gives engines quicker acceleration and smoother operation.
- Enhanced durability: By reducing stress on the engine and enabling consistent performance, rail injectors contribute to the longevity of the engine components.
Applications of Rail Injectors
Rail injectors are versatile components used across a wide range of vehicles and machinery. Some common applications include:
Diesel engines
Found in cars, trucks, and buses, rail injectors help these engines achieve high torque and fuel efficiency.
Agricultural machinery
Tractors and harvesters rely on diesel engines with rail injectors for reliable performance in demanding conditions.
Marine engines
Many ships use diesel engines equipped with rail injectors to handle long hours of operation efficiently.
Generators
Rail injectors ensure stable fuel delivery in diesel generators, which are often used for backup power.
High-performance vehicles
Some petrol engines, especially in sports cars, use rail injectors for enhanced power and precision.
Maintenance and Challenges
While rail injectors are designed to last, regular maintenance is key to ensuring optimal performance. Over time, injectors can become clogged or worn due to impurities in the fuel or high operating pressures. Symptoms of a failing injector include reduced fuel economy, engine misfires, or excessive smoke from the exhaust.
To extend the lifespan of rail injectors:
- Use high-quality fuel to prevent contamination.
- Replace fuel filters regularly.
- Follow the manufacturer’s recommended service intervals.
- Clean or replace injectors if signs of wear appear.
Addressing these issues promptly not only prevents costly repairs but also maintains the performance benefits of the injectors.
Driving Efficiency Forward
Rail injectors are more than just another engine component—they are a cornerstone of modern engine technology. Understanding their importance highlights just how far engine technology has come—and where it’s heading next.